On the way to predominantly e-mobility at BMW and the electric transformation of brands such as Mini and Rolls-Royce, the company is making sustainability a bigger priority and has several technologies and concepts for this and strategies developed to get closer to these goals, especially with the “New Class”.
Table of contents
- 50 percent less cobalt in the cathode
- Everyday consumption figures
- Solid-state batteries ready for series production by 2030
- Higher proportion of secondary material
- Vegan steering wheels from 2023< /li>
- Alternatives to leather under development
- Maritime waste becomes cladding parts
- Green electricity for aluminum and steel production
- Track the CO2 balance of individual components
- Generative design for optimal use of materials
- Sustainability costs a lot of money
- New class starts in the 3 Series and X3 segment
-
The new round cells from BMW with 95 mm here (old in the background)
-
Consumption data according to WLTP and use cases
- < figure class="gallery__figure">
Deserttex made from cactus fibers and bio-based polyurethane matrix
< /ol>
From 2025, the “New Class” will be the next big step at BMW, following the iX and its innovations, and is intended to introduce a new IT and software architecture as well as a new electric drive and battery generation. BMW had already presented the new round-format battery cells used at the beginning of the month. The round cells are manufactured with a standardized diameter of 46 mm and two heights of 95 mm and 120 mm. A distinction is made between the vehicle model and the available space in the underbody, for example in sedans or large SUVs.
50 percent less cobalt in the cathode
< p class="p text-width">The new cells are said to be more environmentally friendly thanks to a 50 percent reduction in the proportion of cobalt in the cathode with a higher nickel content and 20 percent less graphite in the anode with a higher proportion of silicon. The volumetric energy density in the cell increases by more than 20 percent. The company in Munich explains that BMW can save 40 percent on the copper foil for the anode. The manufacturer wants to reduce the price of these 6th generation lithium-ion cells by up to 50 percent to the level of vehicles with modern combustion engines. The CO2 emissions in production should fall by up to 60 percent compared to the 5th generation.
Image 1 of 5
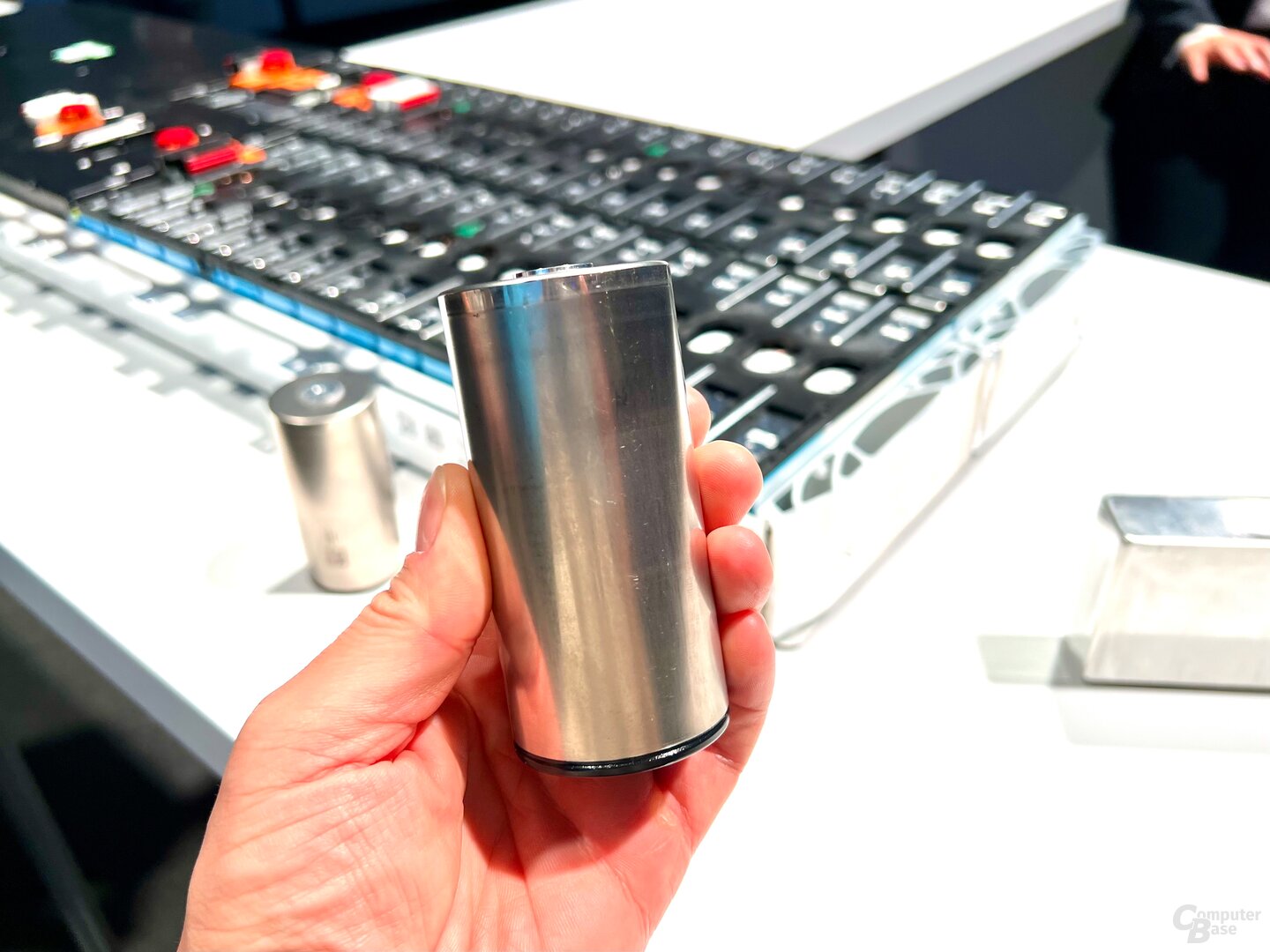
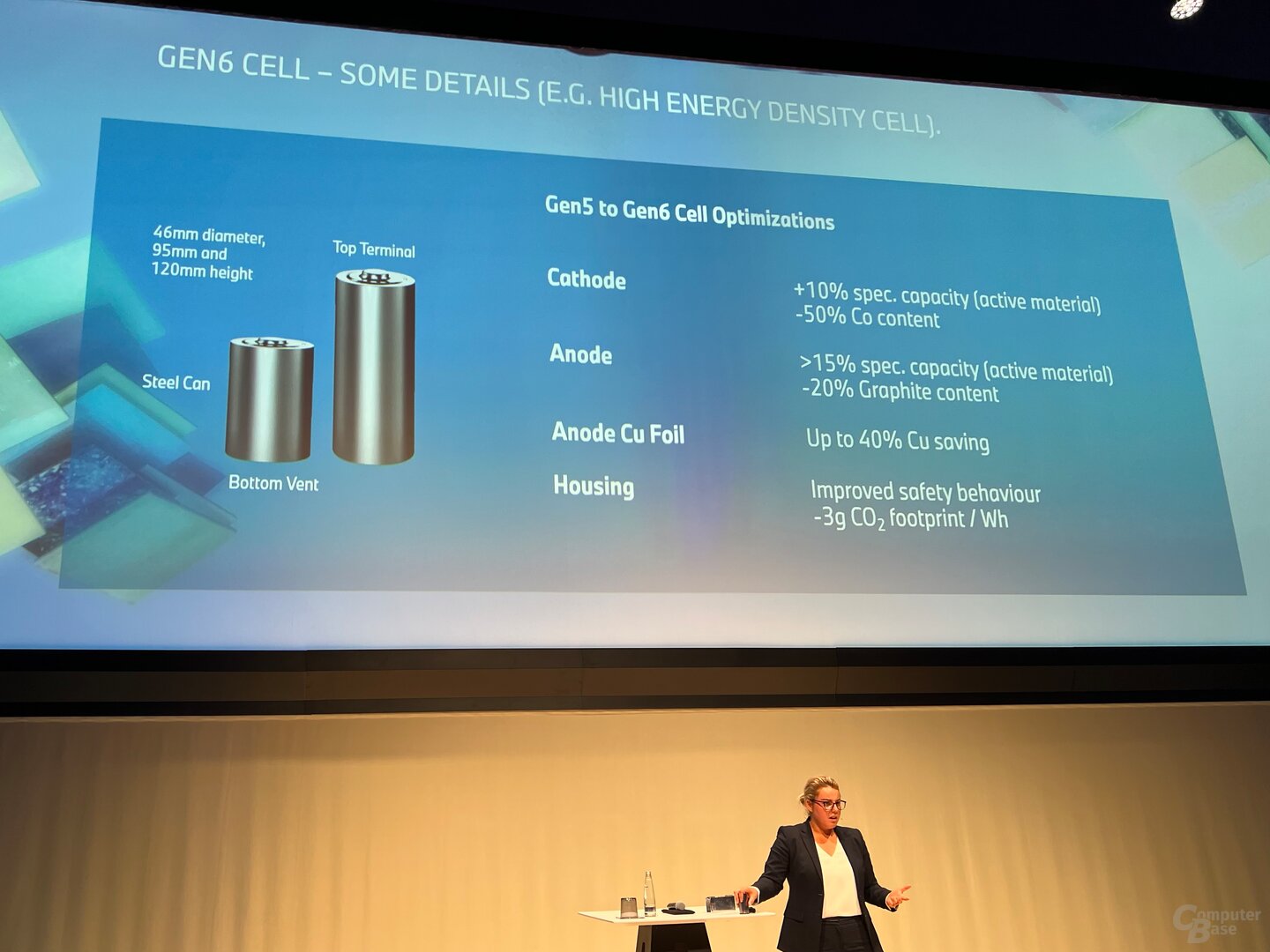

Everyday consumption information
For future buyers, BMW promises up to 30 percent longer ranges (WLTP) and 30 percent faster charging. The “New Class” will have an increased voltage of 800 volts. A significantly increased charging capacity can be achieved at DC fast charging stations with a current of up to 500 amperes. Speaking of WLTP: In the future, BMW also wants to use a “Best Fit” to provide consumption information that is close to everyday life through realistic use cases and test vehicle configurations. The use cases should include dynamic driving situations, long-distance journeys as well as journeys in extreme temperatures and when towing a trailer. The aim is also to depict the vehicles with “customer-representative equipment”.
Image 1 of 3
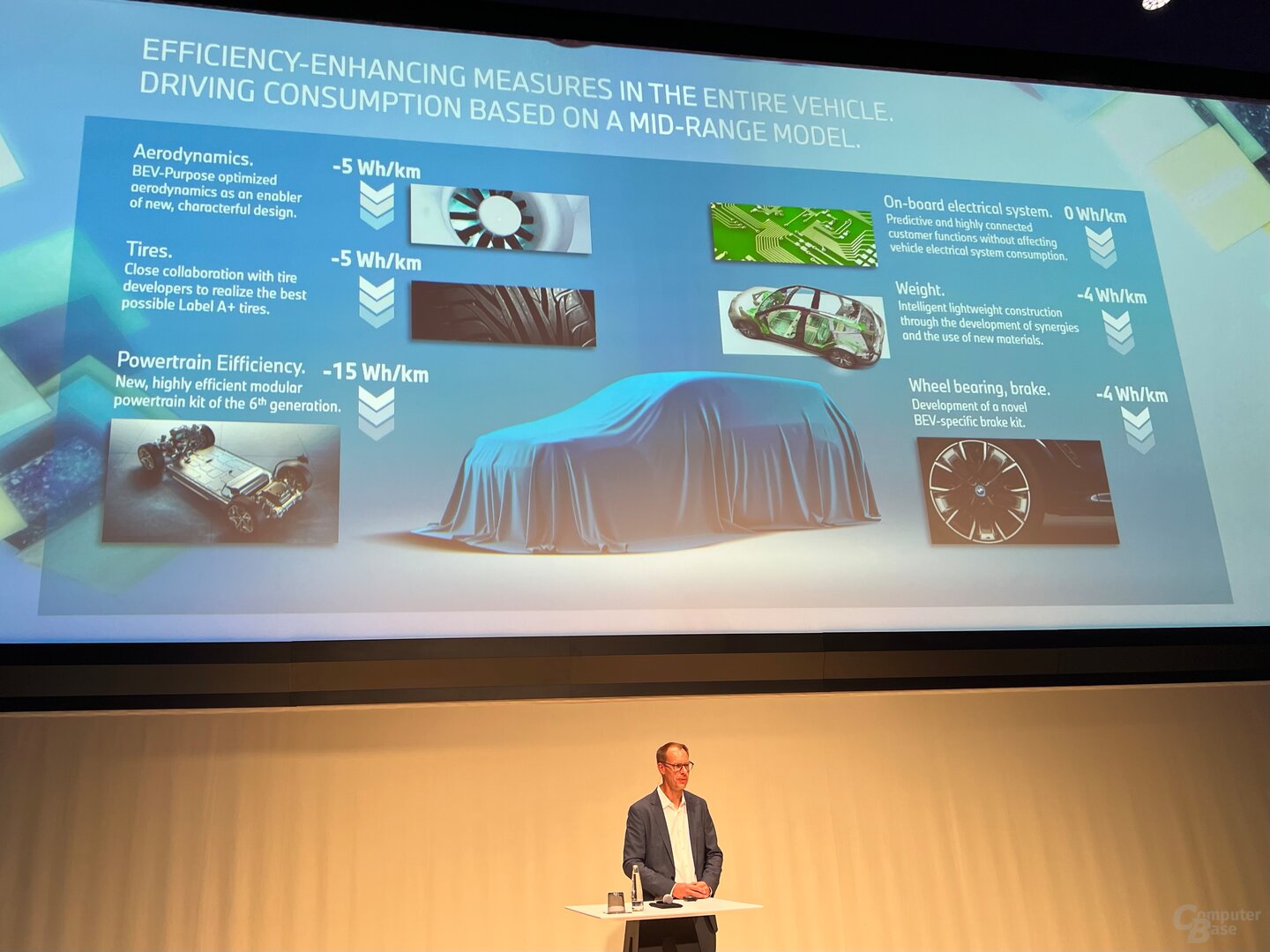
BMW will continue to develop its own battery cells and produce prototypes in the future, but will outsource battery cell production. The company relies on certified mines and wants to ensure responsible mining of the raw materials. To reduce the carbon footprint, cell manufacturers should use cobalt, lithium and nickel, some of which consists of secondary material, and only use green electricity from renewable energies for production, resulting in 60 percent lower CO2 emissions. In the long term, the battery cell should become recyclable, i.e. offer a closed circuit for the reuse of nickel, lithium and cobalt.
Solid-state batteries ready for series production by 2030> h2>
The 6th generation of battery cells also offers the option of using lithium iron phosphate (LFP) cathodes. The raw materials cobalt and nickel in the cathode material can thus be completely dispensed with. In our own competence centers, we continue to work on solid-state batteries, which should be ready for series production by 2030. A vehicle with this technology on board is to be presented “well before 2025”.
Higher proportion of secondary material
Apart from the battery cells, secondary material is also to be increasingly used for the exterior and interior. New recycling processes are to be used, natural fibers are to be used more and alternatives to animal raw materials are to be found. From next year, the group wants to offer completely vegan interiors for the BMW and Mini brands for the first time. BMW expects increasing demand for vegan and leather-free interiors, especially in the USA, China and Europe. Compared to leather, 85 percent of CO2 emissions can be saved along the value chain, explains BMW. 80 percent of the previous emissions are attributable to the methane gas from cattle breeding, another 20 percent to the energy and water-intensive processing of the cattle hide.
Vegan steering wheels from 2023
A last remnant of already largely vegan interiors without leather upholstery is the steering wheel, which places high demands on the material used in terms of appearance, wear resistance and durability. The vegan surface material, which will be available from next year, is designed to withstand wear and tear from abrasion, sweat and moisture. With the help of a prototype for the iX, the editors have already been able to get up close and determine practically no difference to the previous implementation made of leather. The only distinguishing feature of the new material will be a new grain on the steering wheel rim. The vegan steering wheel is used in the basic equipment, but customers will still be able to order real leather for an additional charge. BMW does not want to force any buyer to turn away from animal products, so they are not that consistent. Around 1 percent of animal raw materials will remain in automobiles in the future anyway, for example for waxy substances such as gelatine as a component of protective coatings, lanolin in paints, tallow as an additive in elastomers and beeswax as a flux for paint.
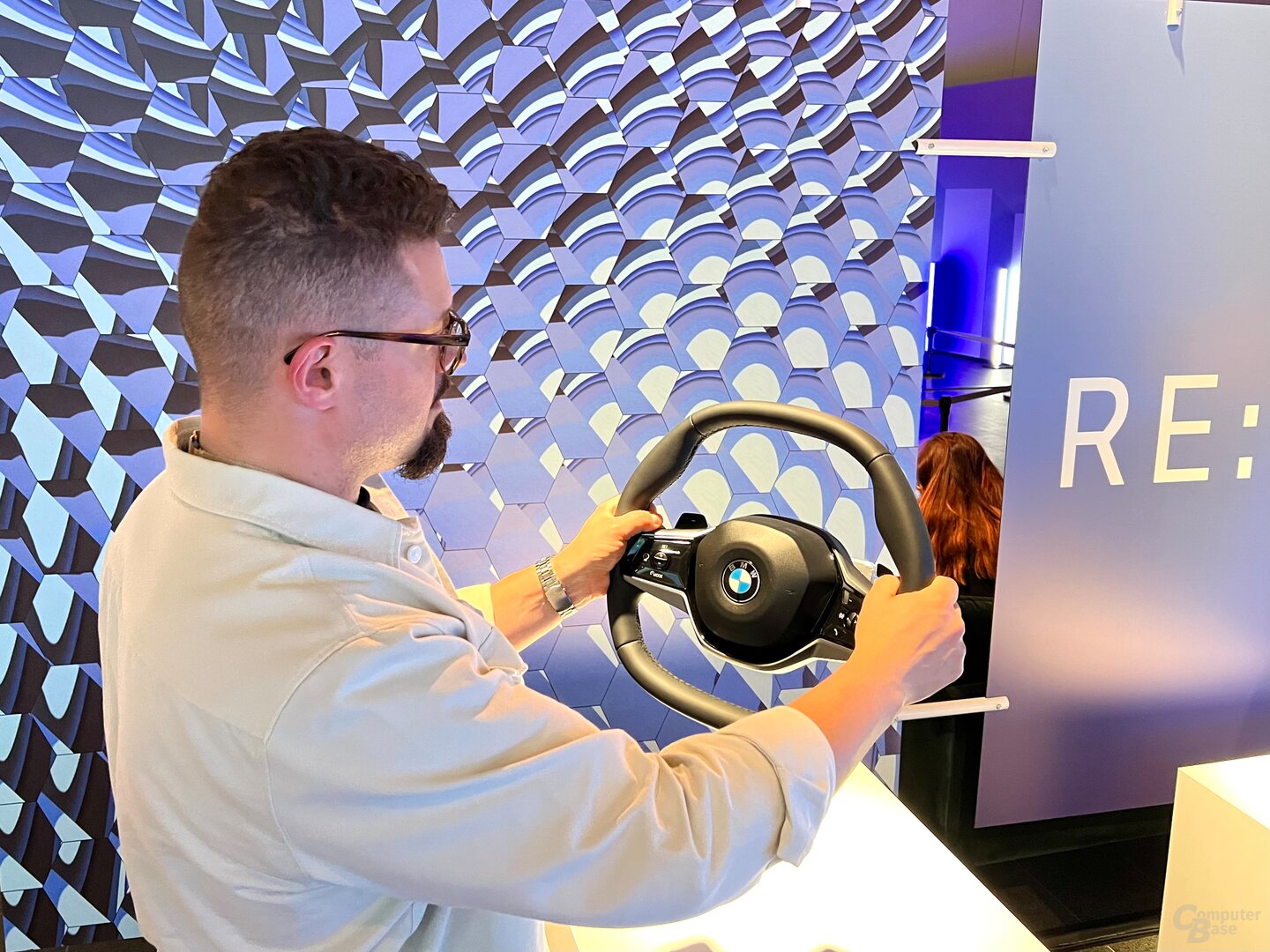
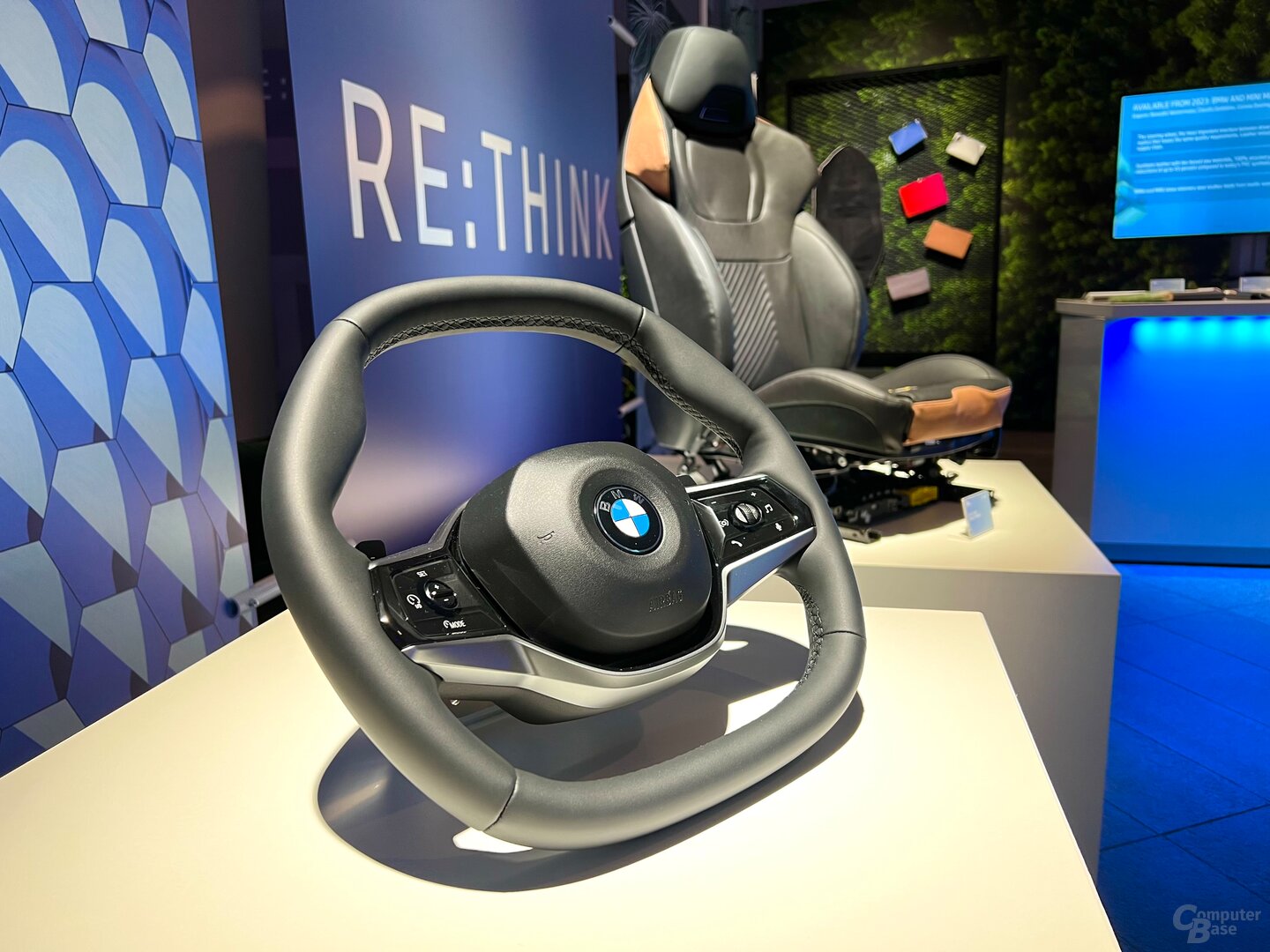
Vegan steering wheel for the BMW iX
The BMW Group wants to achieve climate neutrality by 2050 at the latest. On the way there, seemingly inconspicuous changes, such as the mono-material floor mats already used in production instead of a material mix that is difficult to recycle, also help. The company explains that this saves 23,000 tons of CO2 and 1,600 tons of waste, because recycled floor mats and offcuts can be reused within the production process.
Alternatives to leather under development
With future vehicle generations, BMW intends to offer further alternatives to leather. Mirum is a plant-based material, but it is designed to mimic all the properties of leather. Deserttex, on the other hand, consists of powdered cactus fibers and a bio-based polyurethane matrix. Compared to the leather imitations previously used, CO2 emissions can be reduced by a further 45 percent. At Mini, a vegan interior is planned for the coming model generation, which uses a mono-material made of recycled fibers as the starting material for the complete seat surfaces made of velor fabric, which can be recycled separately. In Munich, BMW showed seat studies made from textile waste, which are processed into a synthetic yarn. This manufacturing process uses around 98 percent less water than using cotton and reduces CO2 emissions by around 80 percent compared to conventional processing of polyester.
Image 1 of 3 < /figure>
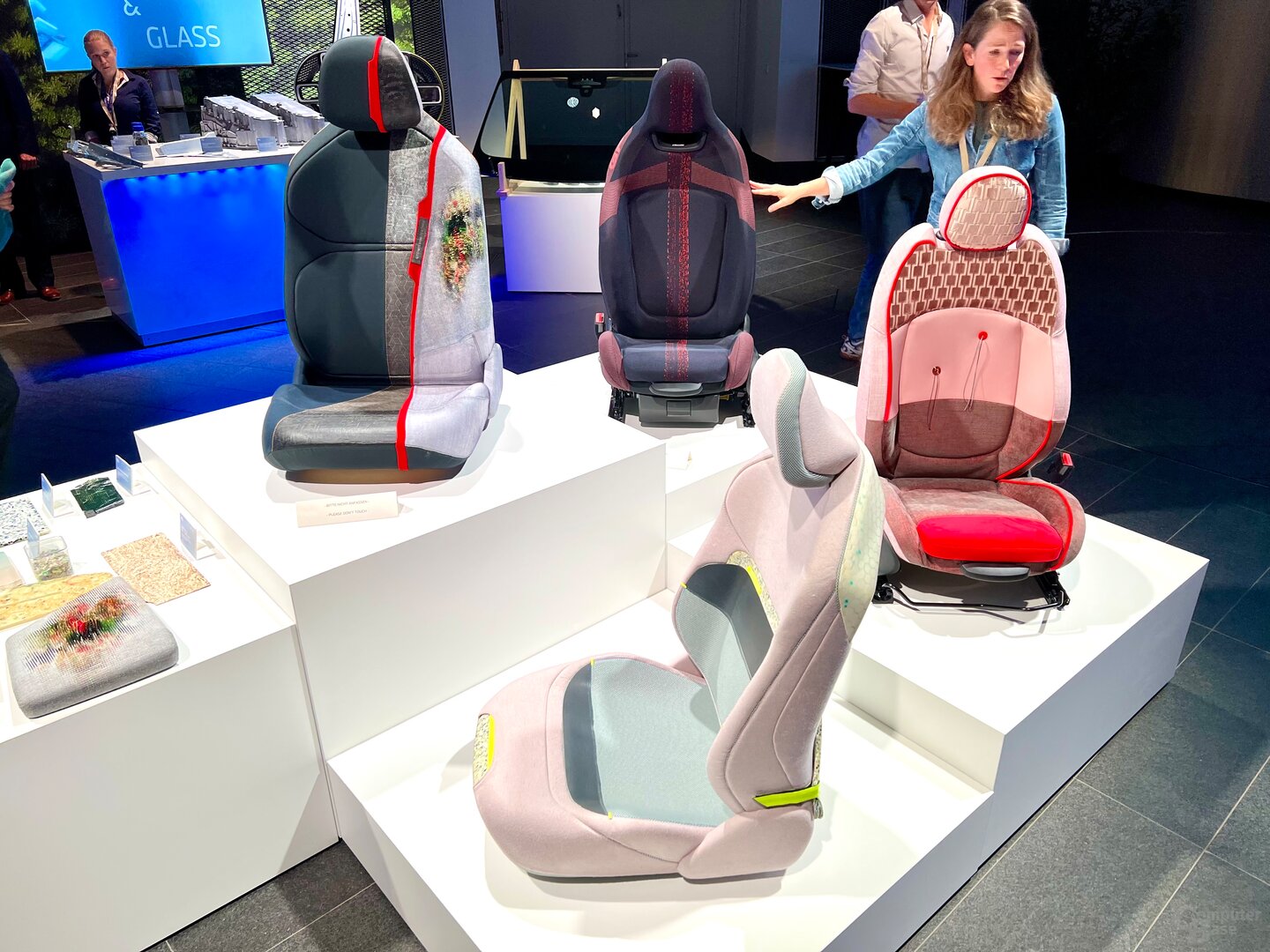

Maritime waste becomes cladding parts
For the first time, the “New Class” planned for 2025 will feature plastic trim parts, the raw material of which consists of around 30 percent recycled fishing nets and ropes. This raw material is proactively sourced from ports around the world to ensure it is not dumped at sea, BMW says. Residues from the maritime industry often end up in the sea instead of being properly disposed of on land. The components used by BMW are said to have a CO2 footprint that is around 25 percent lower than the same components made of conventionally manufactured plastics. Already today, recycled nylon waste forms the basis for a plastic thread from which the floor coverings in the iX and X1 are made. BMW wants to increase the proportion of secondary material in the thermoplastics used from the current level of around 20 percent to an average of 40 percent by 2030.
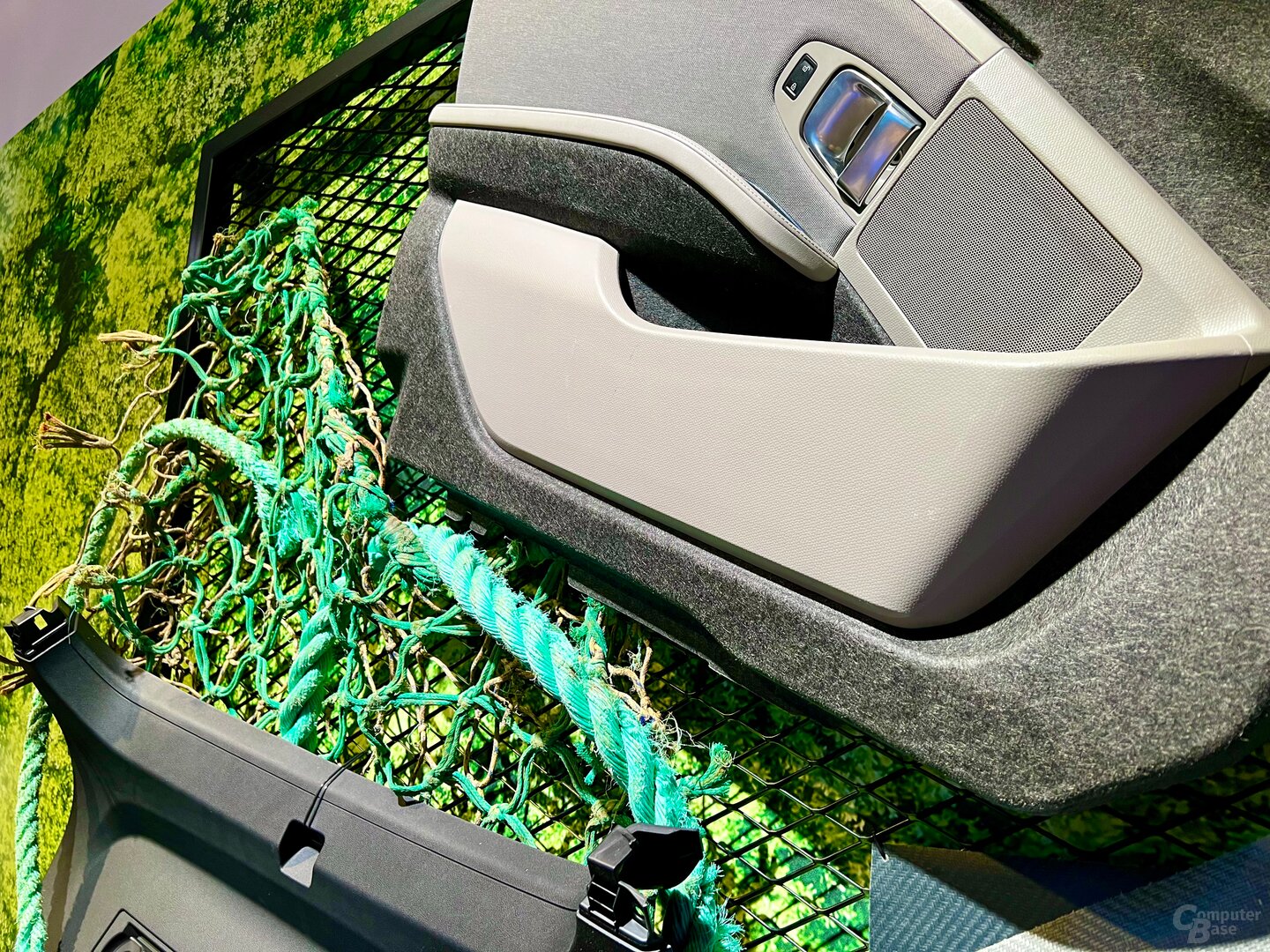
Green electricity for aluminum and steel production
In addition to the secondary material, BMW sees the use of green electricity in aluminum and steel production as an important lever for reducing CO2 emissions. From 2025, steel will also be sourced from a Swedish manufacturer that uses hydrogen and electricity from renewable sources for production. Another company is to supply steel from “CO2-reduced production”, so that more than 40 percent of the requirements for vehicle production in the European BMW Group plants can be covered in this way. This should reduce CO2 emissions by around 400,000 tons per year. Depending on the alloy, secondary raw materials in the steel are to be gradually increased from 25 percent to 50 to 80 percent. In the USA, where all X models are produced, and in China, negotiations are currently still being held with suppliers in order to achieve a CO2 reduction there too.
The production of aluminum leads to significantly higher CO2 emissions, which is far ahead of batteries, plastics and steel in this respect. Since 2021, BMW has been purchasing aluminum produced from green electricity for the first time from the United Arab Emirates, where the light metal is produced using solar power. The company wants to increase the proportion of aluminum produced with green electricity in the long term and emit 2.5 million tons less CO2 by 2030. By 2024, all cast aluminum wheels purchased from the BMW Group are to be produced exclusively with green electricity. This specification includes both the electrolysis in the production of aluminum and the casting of the wheels.
-
Cast aluminum wheels produced exclusively with green electricity
Image 1 of 2 < /figure>
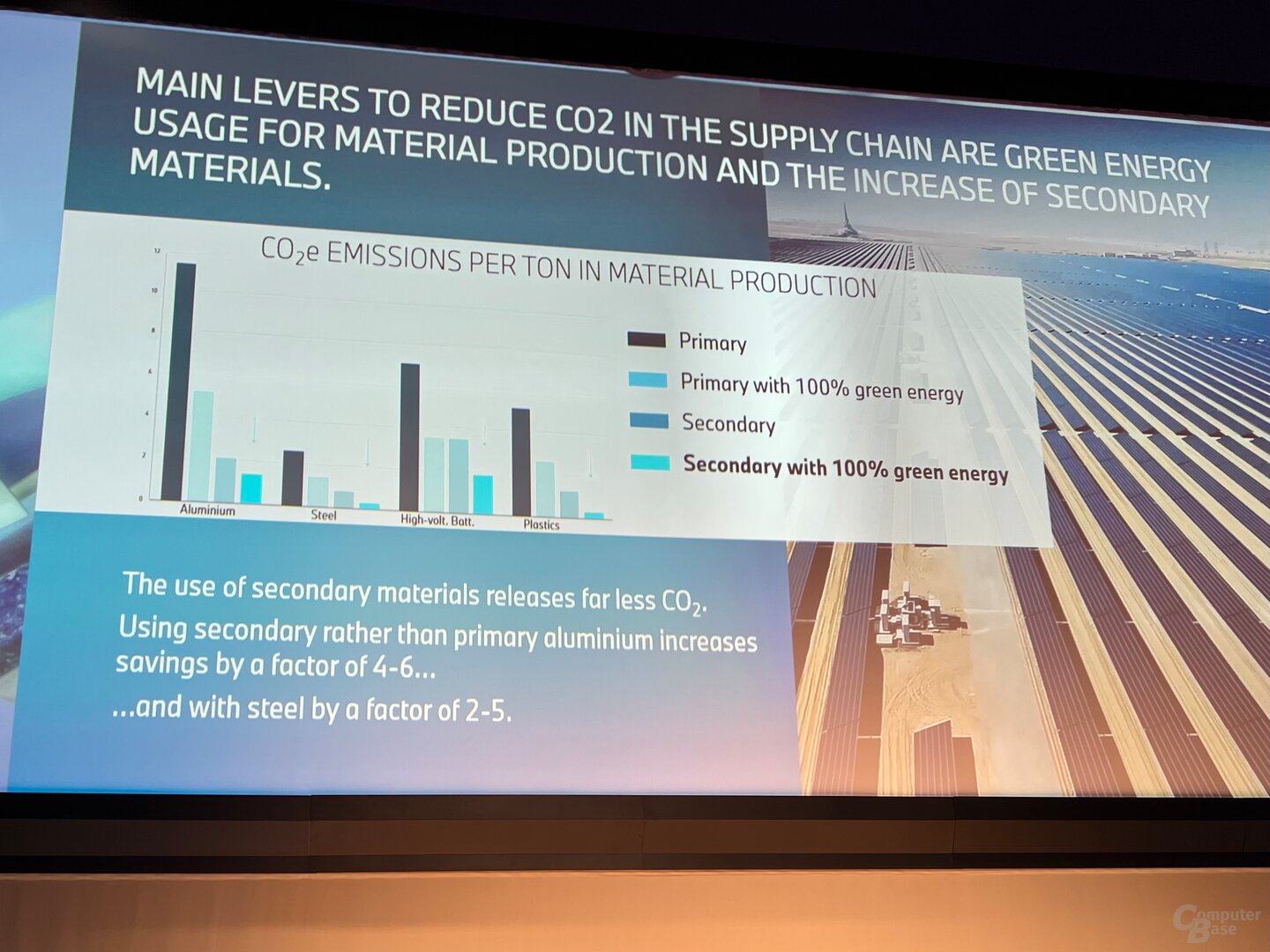
Track the CO2 balance of individual components
BMW is also breaking new ground in the production and development of vehicles. One of these is the Catena-X partner network, which is funded by the federal government and promoted by Economics Minister Robert Habeck, which is intended to create an important basis for establishing a circular economy and the consistent reduction of CO2 emissions in the supply chain by setting up a networked database. Catena-X is intended to enable the secure and anonymous exchange of data between automobile manufacturers, suppliers and IT companies. As an example of the CO2 reduction, the concrete CO2 balance of each individual component can be specified in the network with real data instead of average values. In the supply chain and in vehicle production, credible and comprehensible reporting should be created for the achievement of sustainability goals. In Catena-X, vehicle components can also be fully tracked throughout their entire product life cycle, i.e. from raw material procurement to recycling.
Generative design for optimal use of materials
So-called “generative design” at BMW stands for energy, resource and cost efficiency in the development and production of vehicle components. This is due to the growing automated development of vehicle components, which should establish itself as the standard method in the group by 2025. Structural components with complex geometries can be developed with the support of artificial intelligence in order to achieve optimal use of materials while at the same time meeting the requirements for the component's rigidity, for example. The weight of these components can be up to 50 percent less than conventionally developed components. This type of development can be done conventionally in corresponding programs on a 2D screen, but also in three-dimensional space with the help of a VR headset.
-
AI-supported design of components for optimal use of materials
Image 1 of 2
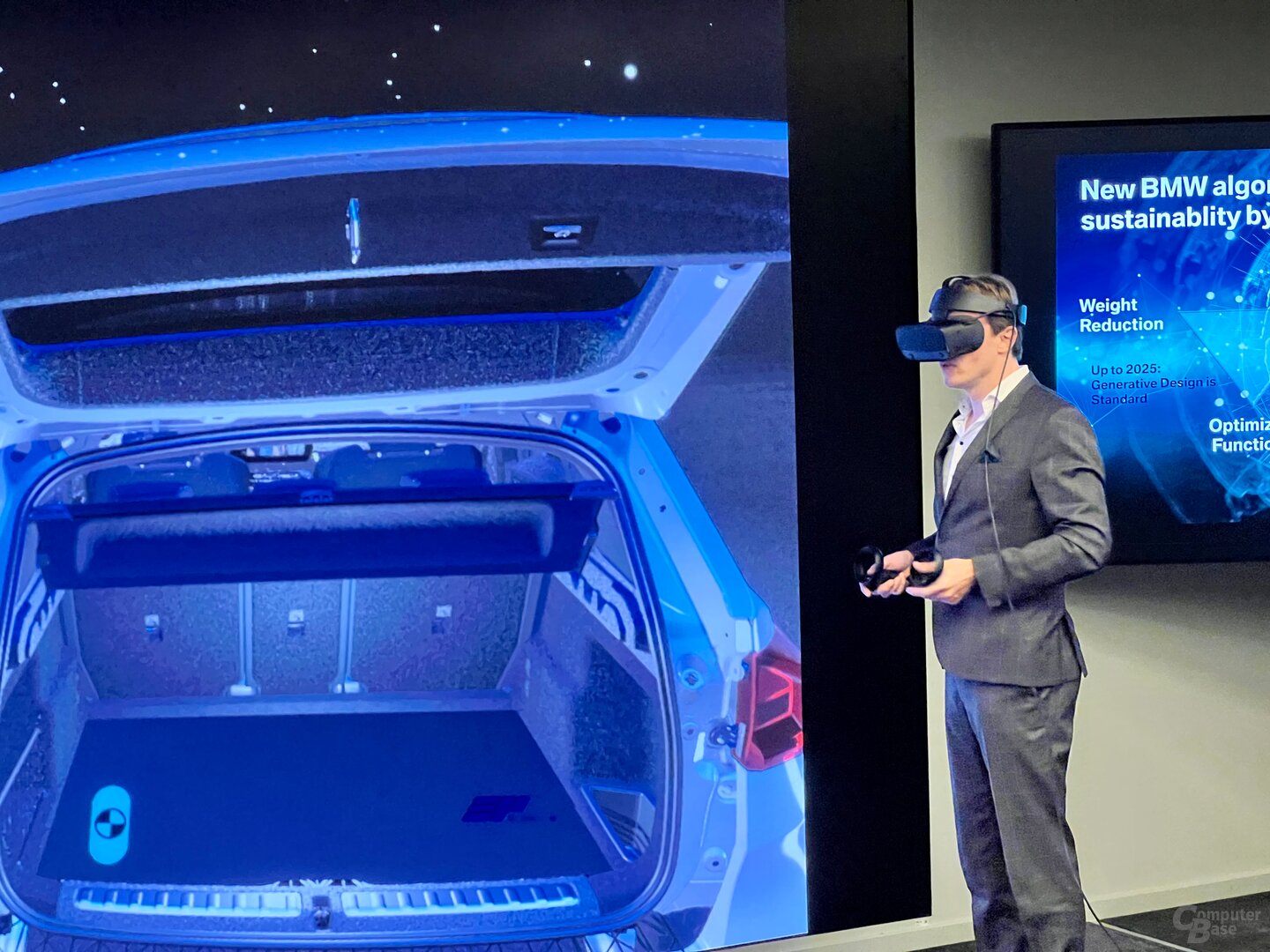
Sustainability costs a lot of money
The company has only revealed to a limited extent what costs BMW will incur as a result of the wide range of developments in the field of sustainability with reference to new battery cell factories. In order to cover the requirements for the “New Class” planned from 2025, the group has awarded a double-digit billion euro amount to the two partners CATL and EVE Energy for the construction of factories. The partners will set up two gigafactories each in China and Europe, which should have a total annual capacity of up to 20 GWh. Two more battery cell factories, for which the partners have not yet been nominated, are to be built in the USMCA region (USA, Mexico, Canada).
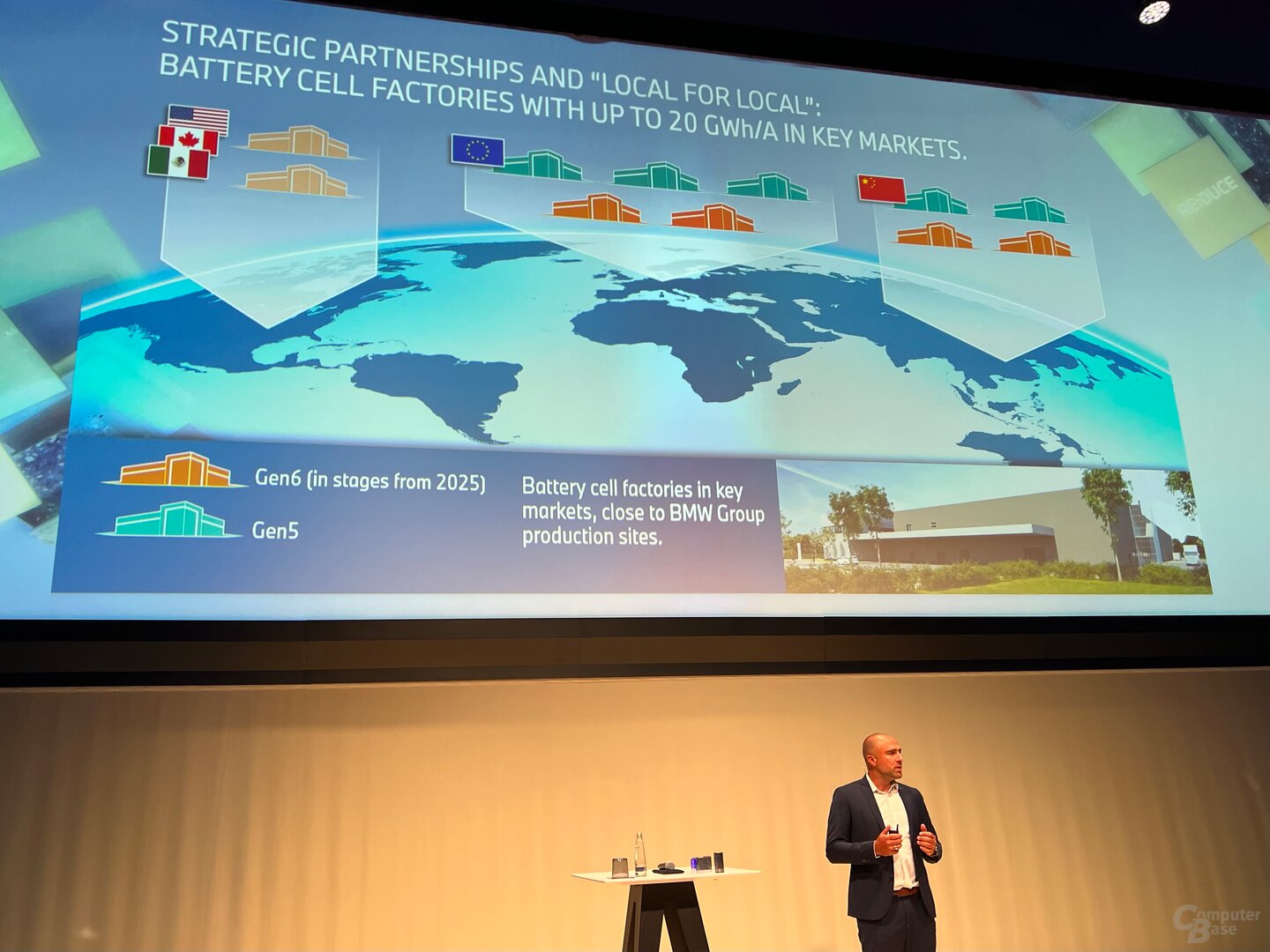
New class starts in the segment of 3 and X3
However, it is not certain that the “New Class” or the first vehicles based on this platform will automatically be located in the luxury segment due to the investments. As Frank Weber, member of the BMW Group Board of Management responsible for development, explained when asked in Munich, the first models are planned in a segment that today serves the 3 Series and X3. This in turn means that these electric vehicles will make a significant contribution to the sales volume of the BMW Group. The “New Class” has the potential to increase the share of all-electric vehicles in global sales to 50 percent by 2030. With the new class, the new platform from the cooperation with Qualcomm and Arriver for driving according to Level 2+ and Level 3 is used for the first time.
By the end of 2025, the BMW Group aims to have more than two million purely electric vehicles on the road. From the beginning of the 2030s, the Mini brand should have an exclusively electric range, the same applies to Rolls-Royce from 2030. At BMW Motorrad, all future new models, at least in the scooter area, should only be electric.
ComputerBase received information about this item from BMW at an event hosted by the manufacturer in Munich under NDA. The costs for arrival and departure were borne by the company. The manufacturer had no influence on or obligation to report. The only requirement was the earliest possible publication date.
This article was interesting, helpful or both? The editors appreciate any support from ComputerBase Pro and disabled ad blockers. More about ads on ComputerBase.