Biler på produksjonsgulvet til et Tesla-anlegg i Austin, Texas. (Jay Janner/Austin American-Statesman via AP, File)
Bilindustrien, som omfatter tusenvis av selskaper, millioner av arbeidere og milliarder i ugjenkallelige kostnader, gjennomgår en endring som skjer én gang i et århundre. I tillegg til å skifte fra vanlige forbrenningsmotorer over mot elektriske kjøretøy, går den også gjennom en ny epoke forandring mens den prøver å takle de globale forsyningskjedeproblemene.
Etter å ha outsourcet mye av produksjonsprosessen det siste halve århundret for å fokusere på design, leverandørstyring og montering av deler, ønsker de store bilfirmaene nå større kontroll over verdikjeden deres – fra metallene som går inn i elbilbatterier til programvaren disse elbilene kjøre på og butikkene de selges i. På sin side, det de ønsker å gjøre er å gjøre EV-armene sine om til teknologiske oppstartsbedrifter.
I Premium Now |For å øke EV-push, batteriløsninger for indisk behov
Men for å forstå hvordan bilprodusenter beveger seg bort fra outsourcing til å internalisere det meste av produksjonen, må vi først forstå hva som har ført til denne enorme, og selvfølgelig dyre, endringen.
Hvordan forsyningskjedekrisen utspant seg.
Skip som står fast til sjøs, varehus som flyter over, lastebiler uten sjåfører: Den svært intrikate og sammenkoblede globale forsyningskjeden var i en omveltning da Covid-19-pandemien rammet. Uroen har avslørt hvordan behovet for å sende kirurgiske masker til Vest-Afrika fra Kina kan ha en gjennomgripende effekt på Fords evne til å sette sikkerhetskameraer på bilene sine ved fabrikker i Ohio og forsinke ankomsten av Amazon Prime-ordrer i Florida.
Best of Express Premium

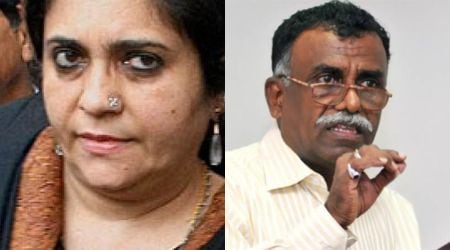
Fresh FIR mot RB Sreekumar, Sanjiv Bhatt og Teesta Setalvad basert på… Etter drapet på Moosewala kan du søke tilbake på (Punjabi) gjenger i Canada IAS offiser sønn død: Avvikene Suraj Yengde skriver: Kasten og politikken til Senas oppgang og dens kriseFlere premiumhistorier >> For hver bil eller lastebil som ikke ruller av et samlebånd i Detroit, Stuttgart, Shanghai eller Manesar, er arbeidsplasser i fare. De kan være gruvearbeidere som graver malm etter stål i Finland, arbeidere som støper dekk i Thailand, eller Maruti Suzuki-ansatte i India som installerer instrumentpaneler – levebrødet til milliarder av mennesker er prisgitt forsyningsmangel og fraktkvelertak som tvang fabrikkene til å begrense produksjonen. Bilindustrien står for rundt 3 prosent av den globale økonomiske produksjonen, og i bilfremstillingsland som Tyskland, Mexico, Japan og Sør-Korea er andelen mye høyere. Sjokkbølgene fra halvlederkrisen, som tvang praktisk talt alle bilprodusenter til å eliminere skift eller midlertidig stenge ned samlebånd, kan være sterke nok til å presse enkelte land inn i resesjon. I Japan, hjemmet til Toyota og Nissan, førte mangel på deler til at eksporten falt med 46 prosent i september 2021 sammenlignet med et år tidligere – en kraftig demonstrasjon av bilindustriens betydning for økonomien. Også i Explained |Why was er det drivstoffmangel i India denne måneden? Bransjeeksperter hadde sagt at bilprodusenter hadde problemer med å få tak i alle slags deler og råvarer av en rekke årsaker, inkludert Covid-relaterte anleggsstans av leverandører, logistiske problemer som involverer mangel på skip, fraktcontainere og lastebilsjåfører, og vanskeligheter som noen leverandører har fyllingsjobber. Industrikonsulent AlixPartners uttalte at forsyningskjedeproblemer fikk bilprodusenter til å bygge 7,7 millioner færre kjøretøy globalt enn de ville ha fått hvis de kunne få alle delene og råvarene de trenger. Da mangelen på halvledere herjet og bilprodusentene tar den elektriske ruten og endrer forsyningskjedene sine, ser det ut til å være det å gjøre alt under ett tak. langt frem. Og det er her begrepet “teslafikasjon” ble til. Teslas industrielle system handler om å internalisere alle aspekter av produksjonen, og derfor all fortjenesten. Elon Musk har hevdet at selskapet hans var “absurd vertikalt integrert” av enhver standard, ikke bare bilindustriens. Og de større bilselskapene ønsker å etterligne det Tesla, verdens ubestridte EV-mester, har gjort. Ikke gå glipp av Explained |Hvorfor flying er i ferd med å få 15 % — eller mer — dyrt Så, hva gjør Tesla? EV-giganten har inngått nylige avtaler med litiumgruvearbeidere og grafittleverandører, og bekreftet i mai 2022 en avtale med Vale, en brasiliansk gruvegigant, om å kjøpe nikkel. Planen er å kjøpe det meste av litium, over halvparten av kobolten og rundt en tredjedel av nikkel direkte fra ni gruveselskaper. Den vil bruke disse mineralene i gigafabrikkene, hvorav den første begynte å lage batterier i 2017 i Nevada i samarbeid med Panasonic i Japan. Den planlegger å lage flere celler på egen hånd ved sine tre andre gigafabrikker rundt om i verden. Tesla har også trukket andre deler av drivverket internt. Den lager sine egne motorer og mye av sin egen elektronikk, noe som gir den mer kontroll over kostnadene så vel som over teknologien. For å legge til dette, designer Tesla også sine egne halvledere, et grep som har hjulpet den klarer den globale brikkemangelen bedre enn rivalene. Teslas programvareingeniører har også laget en sentralisert dataarkitektur for å kjøre på disse brikkene, noe som sikrer jevn integrasjon med maskinvaren. Elon Musk har til og med droppet den forhandlerbaserte salgsmodellen, i stedet åpnet sine egne Tesla-butikker. Og hva er resultatet av dette? En enorm markedsverdi på 724 milliarder dollar, som er nesten like mye som de neste ni store bilprodusentene til sammen. Best of Explained Klikk her for mer De store aktørene i spillet gjør det som har vært en eldgammel praksis – å hale en rival som prøver noe som fungerer. I følge banken UBS representerer “integrering et sterkt konkurransefortrinn i et miljø med strukturelt stramme forsyningskjeder.” I årevis har bilprodusenter outsourcet til store leverandører som Bosch, Continental og Denso for å konsentrere seg om å administrere forsyningskjeder, integrere separate deler, design og markedsføring. Leverandører solgte lignende komponenter til mange kunder ved å bruke skala for å holde prisene lave. Dette frigjorde kapital til bilprodusentene, men fjernet teknologisk innovasjon på ett trinn. Mercedes Benz estimerer verdiøkningen til 70-30 til fordel for leverandørene. Men rammet av den globale forsyningskjedekrisen ønsker de å gjøre det Tesla gjør, dvs. redusere dette forholdet til 50 -50 (tallet er ifølge et estimat fra Jefferies, en investeringsbank) som stiger til fordel for internt. BMW sa i 2021 at de hadde satt inn 334 millioner dollar i et argentinsk litiumprosjekt. I fjor signerte Stellantis og Renault avtaler med Vulcan Energy Resources, og GM avslørte en “investering på flere millioner dollar” i kontrollerte termiske ressurser, i hvert tilfelle for litium. I april inngikk Ford en avtale med Lake Resources for det samme mineralet, mens Stellantis og Mercedes inngikk en avtale med Umicore, en belgisk kjemikaliegigant, om å levere katodematerialer til ACC, de to bilprodusentenes batteri-joint venture. En måned tidligere annonserte BYD, et mer Tesla-lignende kinesisk firma, en investering på nesten 500 millioner dollar i en kinesisk litiumgruvearbeider. Det sies å ha kjøpt seks gruver i Afrika. Nyhetsbrev | Klikk for å få dagens beste forklaringer i innboksen din Arbeidet med å etterligne Teslas batterigigafabrikker begynner også. Volkswagen skaper en viss intern batteriproduksjonskapasitet og har øremerket 2,1 milliarder dollar til sin tyske fabrikk, og sier at de vil bygge seks batterifabrikker i Europa innen 2030. Ford og SK Innovations i Sør-Korea vil forsvinne 7 milliarder dollar og 4,4 milliarder dollar, henholdsvis for tre felles gigafabrikker i Amerika. I fjor avduket GM en investering på 2,3 milliarder dollar for et batterianlegg i Tennessee bygget med LG, et annet sørkoreansk firma. Å kjøpe hyllevare elektriske motorer faller også i unåde. Hyundai og Renault-Nissan-Mitsubishi-alliansen går stort sett alene. BMW, Ford, GM, Mercedes og Volkswagen planlegger å lage flere motorer i sine egne fabrikker. De 7,7 millioner bilene i tapt produksjon i fjor som følge av den globale halvledermangelen har fått industrien til å knytte tettere bånd med brikkedesignere som Qualcomm og Nvidia, som en gang ville ha solgt brikker til firmaer langt nede i bilprodusentenes forsyningskjede.< /p> Les også |Hvorfor er det en verdensomspennende oljeraffinering? Er det noen forrang til dette? Hva Tesla gjør nå, gjorde Henry Ford for flere tiår siden. Han hentet ofte råvarer, som gummi til dekk og stål til chassis, fra plantasjer og masovner som eies av firmaet hans. Hans River Rouge-fabrikk i Detroit ble drevet av kull fra Ford-gruvene. Han var oppbrukt av å lagre nok materialer til å sikre at samlebåndene hans kunne fortsette å fungere uten svekkende mangel. Med internalisering av forsyninger i stedet for outsourcing, ville det definitivt utgjøre tap for leverandører og mer hodepine for bilsjefer og til og med Selv om denne endringen vil fremprovosere tilbakeslag fra regjeringer, ser det ut til at teslafikering er veien videre.Premium
Premium
Premium
Hva gjør andre bilprodusenter?