Building new chip factories is one thing, equipping them is another: Factory outfitters have lead times of up to two years, which not only applies to the latest high-end equipment, but also common ones Tools for 200 mm wafer production.
Instead of three now up to 24 months waiting time
Usually, the lead times between ordering new machines and delivery are three to six months, as it was even last year. The boom in the semiconductor industry and the demand for new factories and greater capacity expansion are not only causing their order books to swell, but also those of factory equipment suppliers and thus the so-called lead time. This is now an average of 14 months, but for systems that are very popular, it is over two years.
Systems that are in great demand come from the well-known factory equipment supplier ASML, among others. According to the report, the highest lead times there are currently not found with EUV scanners, but with classic ArF scanners, i.e. those that still use 193 nm as a light source and then optionally with immersion. These run in the division generally under DUV, EUV is the now popular successor. If, for example, only a few layers are exposed with EUV, it is sufficient for many products to finish the remaining layers with classic DUV systems – this saves money. But DUV is the state of the art, especially in many smaller factories, even with only 200 mm wafers, which is why there is more or more demand for them. ASML recently declared on the topic to expand production in this area by a double-digit rate, because without these machines there would be no more chips for the industry.
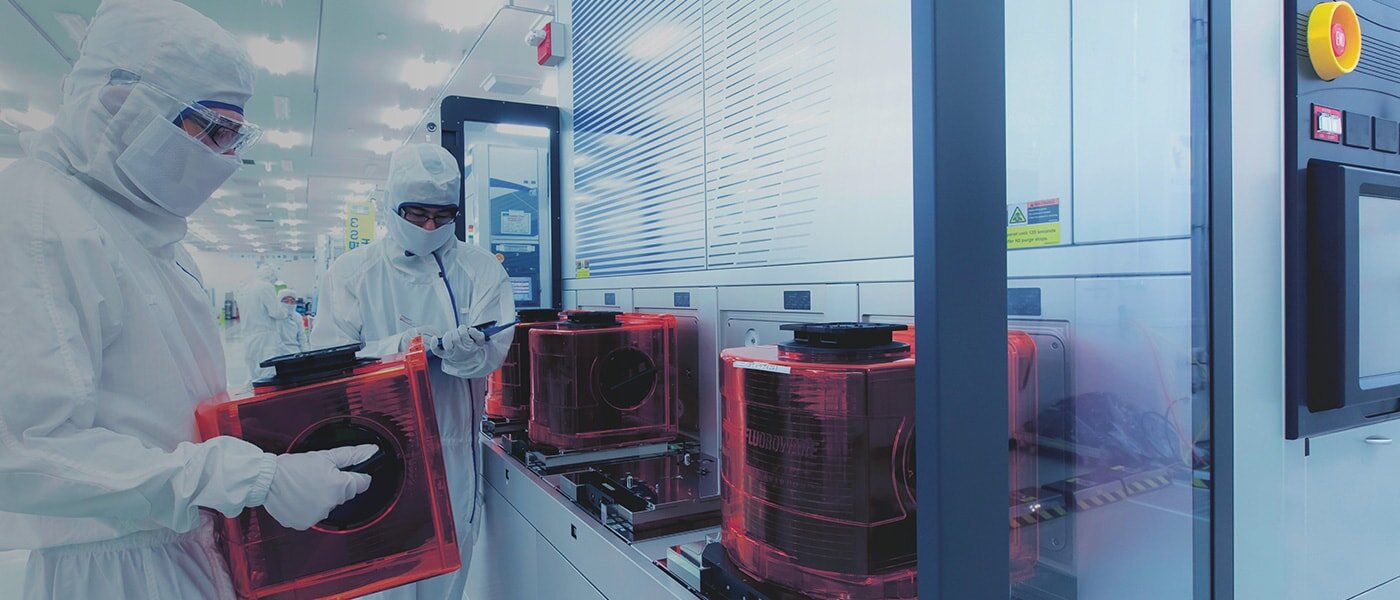
Almost the entire industry is booming
But it's not just the exposure systems, but the complete package on the machines needed in factories from multiple suppliers such as Tokyo Electron (TEL), Hitachi High-Tech, Kokusai Electric, Advantest, Screen Semiconductor Solutions, Kulicke & amp; Soffa, Disco, Varian Semiconductors, Edwards, Applied Materials, even pumps from Ebara and various KLA systems are in short supply.
For new factories this is less of a problem than quickly upgrading existing locations to additional capacity. The former takes a few years anyway, and the rapid expansion of capacity ultimately has a lot of adjustment screws, especially since it is not yet done with the pure tools either. Without the other materials, these cannot be operated, which is why the substrates, which have recently been in high demand, and various other chemicals come into play. Here, too, there are bottlenecks in some cases, and the lack of hydrogen fluoride at Samsung two years ago, when South Korea and Japan were in a trade dispute, is also fondly remembered. At that time, Samsung stated that it would only be able to continue working for a month without deliveries.
An end to the boom is not in sight for the time being. The industry association SEMI expects many new factories to be built and significant sales gains in the coming years, and the forecast for equipment expenditures is also increasing accordingly.